L'acier
d'après Wikipedia
L'acier s'élabore actuellement de deux manières :
- Dans un haut-fourneau, à partir du minerai de fer et de coke avec réduction du carbone dans un convertisseur.
- Dans un four électrique, à partir d'acier de récupération. On parle d'acier de recyclage ou d'acier électrique.
Usine d'agglomération
Le minerai de fer possède des propriétés chimiques et physiques incompatibles qui le rendent inexploitable en l'état par le haut-fourneau. Il lui manque en particulier:
- la résistance mécanique nécessaire pour supporter l'écrasement dû à l'empilage des matières dans le haut-fourneau
- la porosité permettant la circulation du vent des tuyères vers le gueulard
- la composition chimique en oxydes, pour maîtriser le laitier
Les minerais sont préparés par broyage et calibration en grains qui s'agglomèrent entre eux. Le mélange obtenu est cuit sous une hotte à 1 300 °C. L’aggloméré obtenu est ensuite concassé et calibré puis chargé dans le haut-fourneau avec du coke.
Cokerie
De façon simplifiée, le coke est du carbone presque pur doté d'une structure poreuse et résistante à l'écrasement. Il est utilisé comme un puissant réducteur après avoir été libéré des composants indésirables de la houille. Pour cela on l'a fait cuire, à l'abri de l'air, dans les fours de la cokerie à 1 250 °C durant 17 heures. En brûlant dans le haut-fourneau, le coke apporte la chaleur nécessaire à la fusion du minerai et le carbone nécessaire à sa réduction.
Au Creusot, on peut voir les restes des fours à coke sur le jardin de l'Europe en face du Château de la Verrerie.
Haut fourneau
On extrait le fer de son minerai. Minerai et coke solides sont enfournés par le haut, le gueulard. L'air chaud (1 200 °C) insufflé à la base provoque la combustion du coke (carbone presque pur). L'oxyde de carbone ainsi formé va « réduire » les oxydes de fer, c'est-à-dire leur prendre leur oxygène et, de ce fait, isoler le fer. Il se chargera cependant en carbone au fur et à mesure de sa descente dans le haut-fourneau et se transformera en fonte. À la sortie d'un haut-fourneau ces oxydes sont recupérés à l'état liquide, avec la gangue du minerai. Leur densité moindre les fait flotter au-dessus de la fonte. Ce résidu est appelé laitier du haut-fourneau et est principalement exploité pour la fabrication du ciment.
|
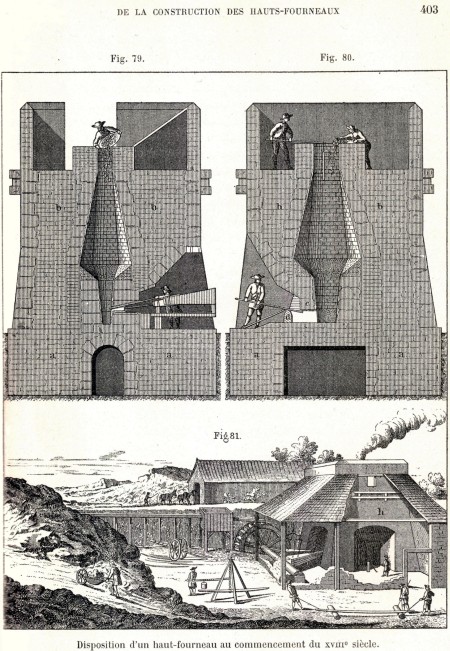
Représentation d'un haut fourneau fin XVIIe siècle.
Sur la coupe en haut à gauche (fig. 79), on distingue un soufflet
et sur la coupe en haut à droite, le trou de coulée (fig. 80)
|
Création et développements du haut-fourneau
d'après Wikipedia |
Les premiers à avoir développé le haut fourneau furent les chinois.
Au cours du XIVe siècle, la force hydraulique est appliquée pour la ventilation des foyers ou bas fourneaux utilisés pour extraire le fer du minerai. L'utilisation de roues à aubes ou à godets en remplacement de la force humaine permet d'augmenter la puissance des vents. Ceci permit l'augmentation de la hauteur des fours jusqu'à atteindre quatre à cinq mètres. Avec un fourneau de cette hauteur et les températures permises par les nouveaux soufflets, le fer une fois réduit se combinait au carbone, produisant de la fonte, dont la température de fusion (environ 1 200 °C) est nettement inférieure à celle du fer pur. On obtenait donc de la fonte liquide au bas du fourneau, et non plus la loupe de fer pâteux qu'il fallait jusque là extraire du fourneau pour l'amener à forger.
En Europe, le lieu et la date précise d'apparition des hauts fourneaux ne sont pas encore établis avec certitude ; ils semblent avoir été connus au XIVe siècle dans la région de Liège ; des structures fouillées en Suède ainsi qu'en Westphalie, datée du XIIIe siècle pourraient également être des fourneaux de ce type. Ils se généralisent au XVe siècle dans la plus grande partie de l'Europe du Nord.
|
Hauts fourneaux d'Anzin, avant la Première Guerre mondiale |
La conséquence majeure de la production de fonte est que les hauts fourneaux peuvent fonctionner en continu, la fonte étant périodiquement coulée, alors que le bas fourneau doit être arrêté pour extraire la loupe qui s'y est formée. Au XVIIIe siècle, la durée d'allumage des hauts fourneaux allait généralement de cinq à neuf mois en fonction de la disponibilité de l'énergie hydraulique ; ils étaient rechargés par le gueulard en charbon de bois, minerai et castine ; la fonte était coulée une à deux fois par jour.
En 1709 a lieu la première coulée au coke au Royaume-Uni à Coalbrookdale (Shropshire) par Abraham Darby (1678–1717). Le coke remplace le charbon de bois dans l'alimentation du fourneau. Le procédé au coke est perfectionné par le fils et petit-fils de Abraham Darby (qui s'appellent également Abraham Darby). Cependant, la fonte produite de cette manière est dans un premier temps impropre à l'affinage (décarburation pour produire du fer forgé), ce qui explique qu'à cette époque l'utilisation du coke ne se généralise pas. En 1760, le Royaume-Uni ne compte que dix-sept hauts fourneaux au coke et ce n'est qu'en 1780 que son usage se généralise.
En France, les premiers essais au coke n'ont lieu qu'en 1769 à Hayange (aujourd'hui dans le département français de la Moselle) avant que soient construits, sous la direction du Britannique William Wilkinson, les hauts fourneaux au coke du Creusot. Cette production peine cependant à concurrencer la production traditionnelle au charbon de bois : elle ne la dépasse qu'en 1853, à la faveur de l'explosion de la demande due au développement du chemin de fer. En 1860, encore un tiers de la fonte française est produite dans des hauts fourneaux au charbon de bois.
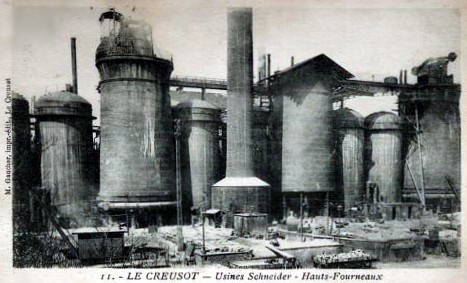
Le Creusot - Les Hauts-fourneaux (collec. perso)
|
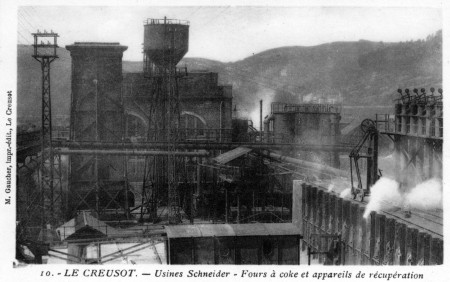
Le Creusot - Fours à coke début du XXème siècle (collec. perso)
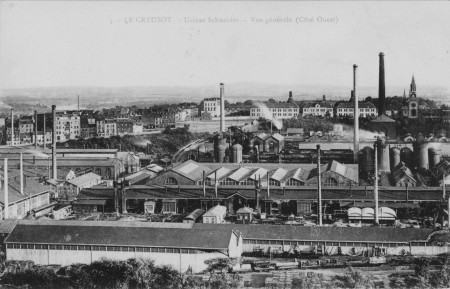
Le Creusot - Vue générale des usines - Hauts-fourneaux à droite (collec. perso)
|
Hommage aux puddleurs
Il existe au creusot une "rue des puddleurs". Si les anciens savent pourquoi cette rue porte ce nom, bien des creusotins actuels n'ont aucune idée de la provenance de ce nom. Alors en compagnie de Jules Vernes, parcourons les lignes de son roman "Les cinq cents millions de la Begum" et découvrons ce métier autrefois exercé au Creusot dans des conditions bien difficiles...
Jules Vernes - Les cinq cents millions de la Begum
- Commencez-vous aujourd'hui?
- Pourquoi pas?
- Ce ne sera qu'une demi-journée ", fit observer le contremaître en guidant Schwartz vers une galerie intérieure. Tous deux suivirent un large couloir traversèrent une cour et pénétrèrent dans une vaste halle, semblable, par ses dimensions comme par la disposition de sa légère charpente, au débarcadère d'une gare de premier ordre.
Schwartz, en la mesurant d'un coup d'oeil, ne put retenir un mouvement d'admiration professionnelle. De chaque côté de cette longue halle, deux rangées d'énormes colonnes cylindriques, aussi grandes, en diamètre comme en hauteur que celles de Saint-Pierre de Rome, s'élevaient du sol jusqu'à la voûte de verre qu'elles transperçaient de part en part. C'étaient les cheminées d'autant de fours à puddler maçonnés à leur base. Il y en avait cinquante sur chaque rangée.
À l'une des extrémités, des locomotives amenaient à tout instant des trains de wagons chargés de lingots de fonte qui venaient alimenter les fours. À l'autre extrémité, des trains de wagons vides recevaient et emportaient cette fonte transformée en acier. L'opération du " puddlage " a pour but d'effectuer cette métamorphose.
Des équipes de cyclopes demi-nus, armés d'un long crochet de fer s'y livraient avec activité.
Les lingots de fonte, jetés dans un four doublé d'un revêtement de scories, y étaient d'abord portés à une température élevée. Pour obtenir du fer, on aurait commencé à brasser cette fonte aussitôt qu'elle serait devenue pâteuse. Pour obtenir de l'acier ce carbure de fer, si voisin et pourtant si distinct par ses propriétés de son congénère, on attendait que la fonte fût fluide et l'on avait soin de maintenir dans les fours une chaleur plus forte.
Le puddleur alors, du bout de son crochet, pétrissait et roulait en tous sens la masse métallique; il la tournait et retournait au milieu de la flamme; puis, au moment précis où elle atteignait, par son mélange avec les scories, un certain degré de résistance, il la divisait en quatre boules ou " loupes " spongieuses, qu'il livrait, une à une, aux aides-marteleurs.
C'est dans l'axe même de la halle que se poursuivait l'opération. En face de chaque four et lui correspondant, un marteau-pilon, mis en mouvement par la vapeur d'une chaudière verticale logée dans la cheminée même, occupait un ouvrier " cingleur ". Armé de pied en cap de bottes et de brassards de tôle, protégé par un épais tablier de cuir masqué de toile métallique, ce cuirassier de l'industrie prenait au bout de ses longues tenailles la loupe incandescente et la soumettait au marteau.
Battue et rebattue sous le poids de cette énorme masse, elle exprimait comme une éponge toutes les matières impures dont elle s'était chargée, au milieu d'une pluie d'étincelles et d'éclaboussures. Le cuirassier la rendait aux aides pour la remettre au four et, une fois réchauffée, la rebattre de nouveau. Dans l'immensité de cette forge Monstre, c'était un mouvement incessant, des cascades de courroies sans fin, des coups sourds sur la basse d'un ronflement continu, des feux d'artifice de paillettes rouges, des éblouissements de fours chauffés à blanc.
Au milieu de ces grondements et de ces rages de la matière asservie, l'homme semblait presque un enfant. De rudes gars pourtant, ces puddleurs! Pétrir à bout de bras, dans une température torride, une pâte métallique de deux cents kilogrammes, rester plusieurs heures l'oeil fixé sur ce fer incandescent qui aveugle, c'est un régime terrible et qui use son homme en dix ans. Schwartz, comme pour montrer au contremaître qu'il était capable de le supporter, se dépouilla de sa vareuse et de sa chemise de laine, et, exhibant un torse d'athlète, sur lequel ses muscles dessinaient toutes leurs attaches, il prit le crochet que maniait un des puddleurs, et commença à manoeuvrer voyant qu'il s'acquittait fort bien de sa besogne, le contremaître ne tarda pas à le laisser pour rentrer à son bureau.
Le jeune ouvrier continua, jusqu'à l'heure du dîner, de puddler des blocs de fonte. Mais, soit qu'il apportât trop d'ardeur à l'ouvrage, soit qu'il eût négligé de prendre ce matin-là le repas substantiel qu'exige un pareil déploiement de force physique, il parut bientôt las et défaillant. Défaillant au point que le chef d'équipe s'en aperçut. " vous n'êtes pas fait pour puddler mon garçon, lui dit celui-ci, et vous feriez mieux de demander tout de suite un changement de secteur, qu'on ne vous accordera pas plus tard. " Schwartz protesta. Ce n'était qu'une fatigue passagère! Il pourrait puddler tout comme un autre!...
|
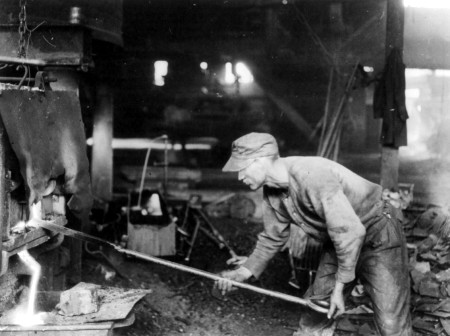
Puddler |
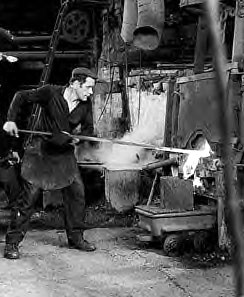
Puddler |
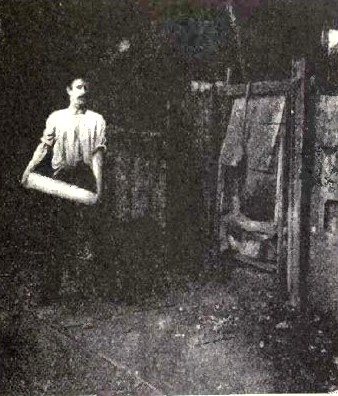
Chargement des brames dans le four à puddler |
|
|
|
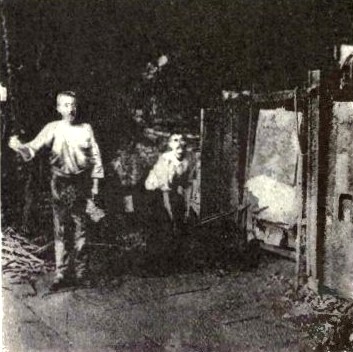
Extraction de la balle de fer |
|
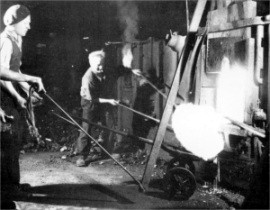
Extraction de la balle de fer |
|